When it comes to cleaning waste oil using a centrifuge, using an inline heater in your setup will make a significant difference. Typically, oil is heated within the range of 170°F to 200°F for optimal performance. However, the specific temperature at which the heater should be set depends on the flow rate of your oil. The quicker your flow rate the higher the temperature on the heater to adequately heat the oil.
If you do not use a heater when processing waste motor oil it is highly recommended to dilute the viscosity of the oil with diesel. Never mix vegetable oil with diesel fuel, the two oils will separate and cause issues when using the fuel.
Here are the top reasons an inline oil heater should be used:
1. Better separation of contaminants: A heater enables the centrifuge to effectively capture debris in the oil, significantly boosting its efficiency in a single pass.
2. Increased production rate: By incorporating a heater, you can ramp up the rate at which you process oil, leading to improved efficiency overall.
3. Water content reduction: Heating the oil facilitates the evaporation of water content reducing the water content present in the oil.
Our inline heater is designed to bolt seamlessly to the leg of the centrifuge, offering both 120V and 240V options for your convenience. To optimize its performance, ensure that the oil is fed into the bottom port of the heater, with the output directed into the centrifuge at the top. This setup prevents the heater element from burning out as it remains consistently submerged in oil. Never use a hose from the heater feeding the centrifuge that is not rated for heat.
Integrating an inline heater into your oil centrifuge setup is a smart move. Not only does it improve debris capture efficiency and processing rates, but it also helps reduce water content, ensuring cleaner oil output for your operations.
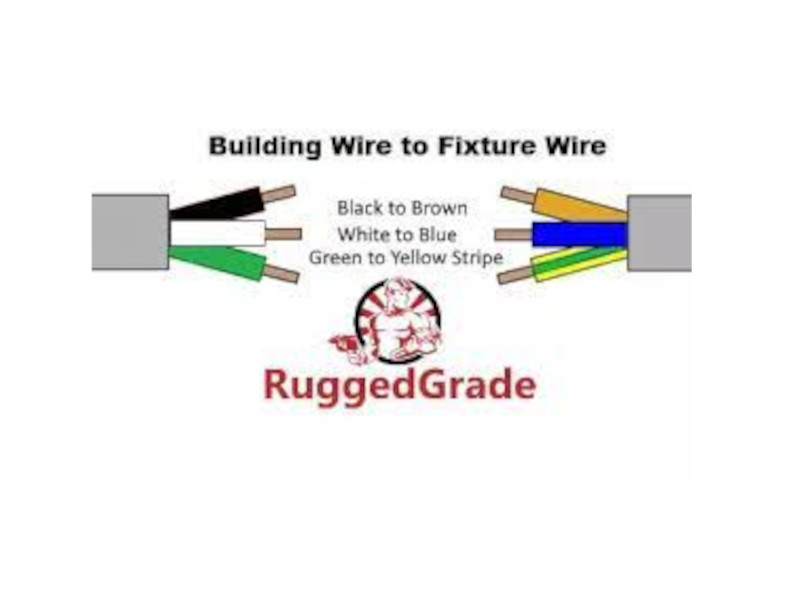
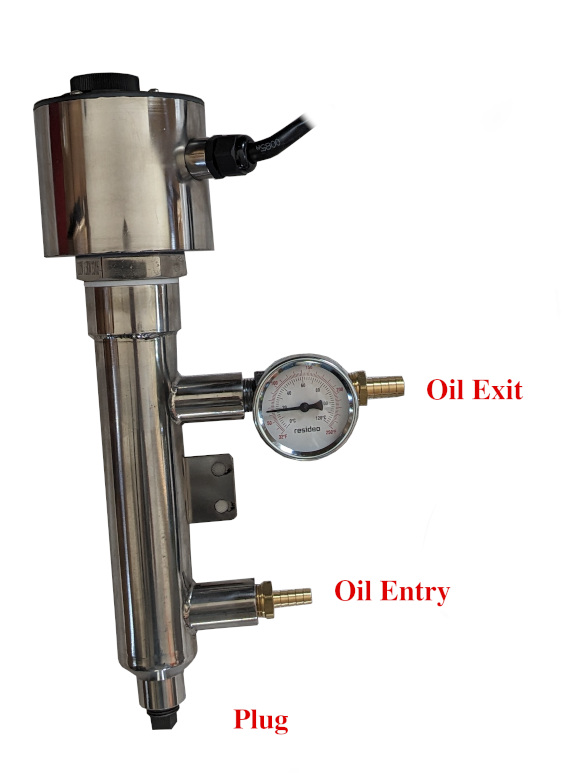