Perfect Your Waste Oil Centrifuge Flow Rate for Cleaner Fuel
When cleaning waste oil with a centrifuge, flow rate is one of the most important things to get right. Many people think faster is better, but that’s not true when it comes to producing clean fuel. Understanding flow rate will help you get the best results from your Ultimate Force Centrifuge.
Why Flow Rate Really Matters
Think of your centrifuge like a washing machine for oil. The longer the dirty oil stays inside the spinning bowl, the cleaner it becomes. The powerful centrifugal force has more time to pull out dirt, water, and other contaminants without fighting against oil trying to escape too quickly.
For making vehicle fuel, we recommend running at 5 gallons per hour (GPH). This slower speed gives the centrifuge time to do its job properly. If you’re cleaning oil for other uses like oil burners, you can speed it up to 10 GPH and still get good results. The Ultimate Force Centrifuge does have a flow rate rated up to 30 GPH, but you sacrifice oil purity and will remove fewer contaminants.
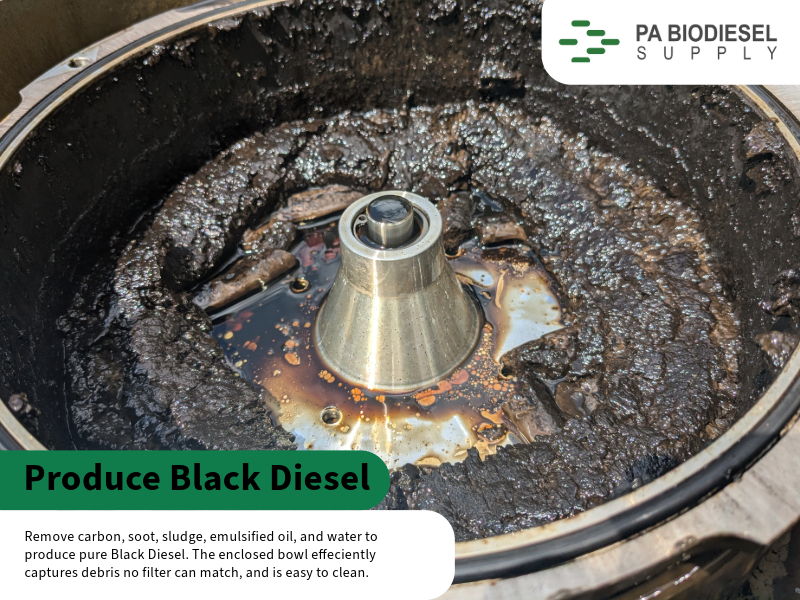
How Flow Rate Actually Works
Inside your centrifuge bowl, two forces are working against each other. The spinning creates a strong centrifugal force that pushes dirt and contaminants to the bowl walls. At the same time, the flowing oil creates an opposing force trying to escape. When you rush the flow, you make it harder for the centrifugal force to do its job effectively.
The Ultimate Force Centrifuge creates 1,657 times the force of gravity (1,657 G-Force). At a 5 GPH flow rate, your oil experiences this powerful force for a full 6 minutes. That’s plenty of time to settle out even the smallest particles.
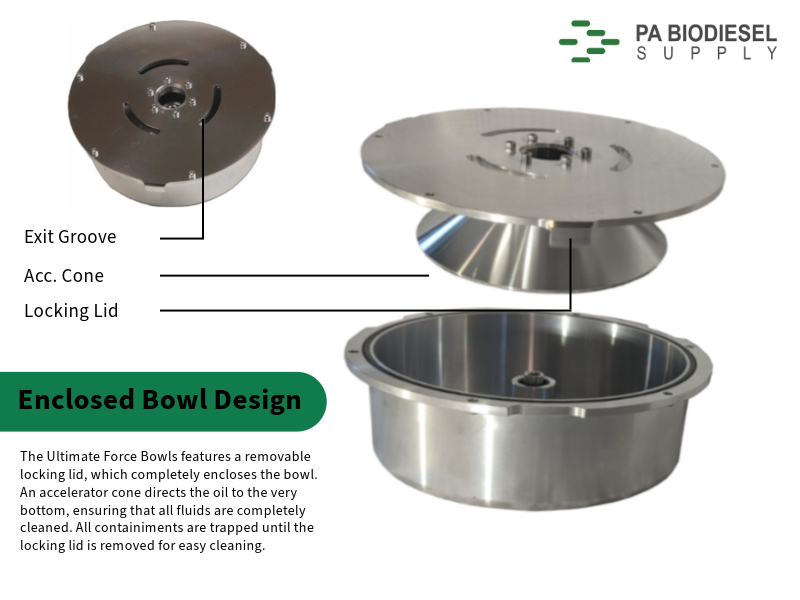
Measuring Your Flow Rate is Simple
You don’t need fancy equipment to check your flow rate. All you need is a quart jar and a timer. Here’s the easy way to figure it out:
First, multiply your target flow rate by 4 (since there are 4 quarts in a gallon). Then divide 60 minutes by that number.
For example, if you want 5 GPH:
- 5 gallons × 4 quarts = 20 quarts per hour
- 60 minutes ÷ 20 quarts = 3 minutes to fill one quart
Here’s a quick reference for different flow rates:
- 2.5 GPH = 6 minutes per quart
- 5 GPH = 3 minutes per quart
- 7.5 GPH = 2 minutes per quart
- 10 GPH = 1.5 minutes per quart
- 15 GPH = 1 minute per quart
Why Heating Makes a Difference
When your oil contains water or is thick and gummy, flow rate becomes even more important. The inline heater needs time to warm the oil to 160°-220°F. This heat evaporates water and makes the oil flow better through the system. Just like hot engine oil drains faster than cold oil, heated oil in your centrifuge separates contaminants more effectively. If you rush the process, you won’t give the heater enough time to work properly.
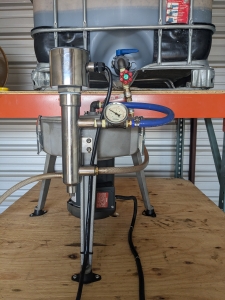
Factors That Affect Your Flow Rate
The height and size of your oil container affects flow rate more than most people realize. A full 55-gallon drum creates about 1.2 psi of pressure at the bottom. Larger 275 or 330-gallon totes can create 2.5 to 3 psi of pressure.
As your container empties, this pressure drops and your flow rate slows down. Each foot of height above your centrifuge adds roughly 0.38 psi of pressure. A drum placed 5 to 8 feet above your centrifuge will maintain a steadier flow rate.
Using a larger input hose between 5/8″ and 1″ diameter also helps by reducing friction. This is especially helpful if your oil cools as it moves through longer feed lines.
Setting Up Your Flow Control
To control your flow rate properly, use two valves. Set up a gate valve to adjust the flow rate and a ball valve to turn the flow on and off. This way, you don’t have to readjust your flow rate every time you start the centrifuge. In the picture below, you can see that we used two valves.
Pre-heating your oil before it enters the centrifuge will give you cleaner results and help it flow better, especially in cold weather. This simple step can make a big difference in how well your system works and the purity of your oil. We always recommend an inline heater when using a centrifuge.
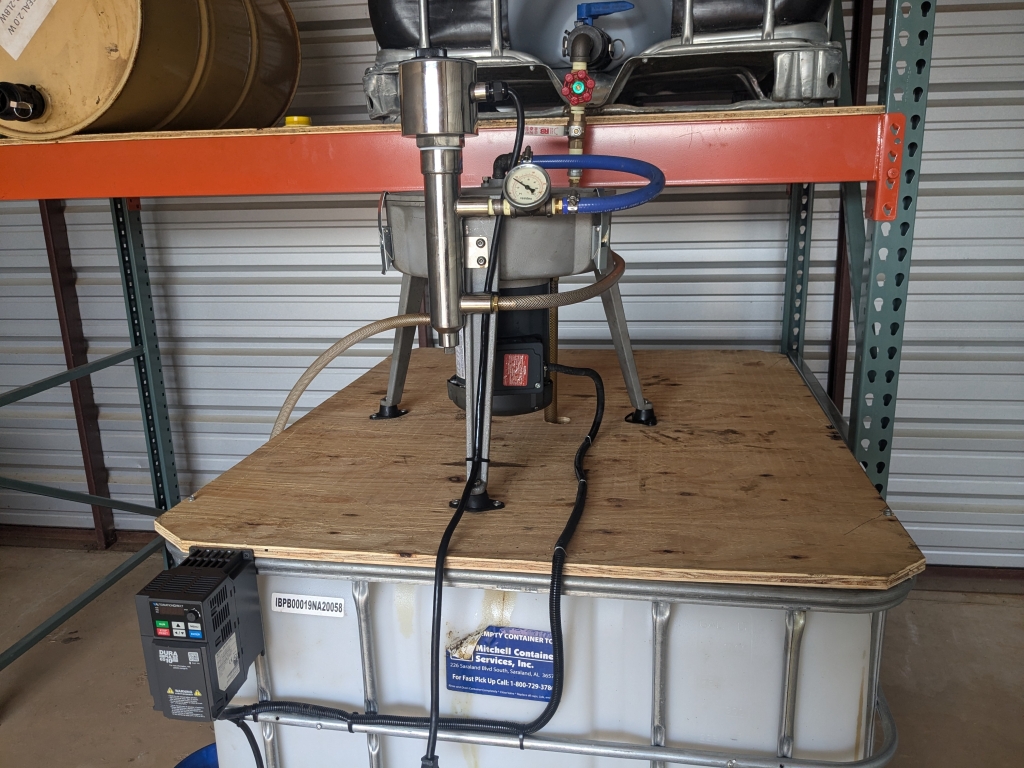
The Slower the Oil, the Cleaner It Will Be
Remember this simple rule: slower flow rate equals cleaner oil. Taking the time to set up your centrifuge at the right flow rate will pay off with cleaner fuel. Your engines will run smoother, and you’ll save thousands of dollars on fuel costs.
Whether you’re processing a few gallons or hundreds, patience with the flow rate is your key to success. The Ultimate Force Centrifuge is designed to give you the best results when you follow these guidelines.